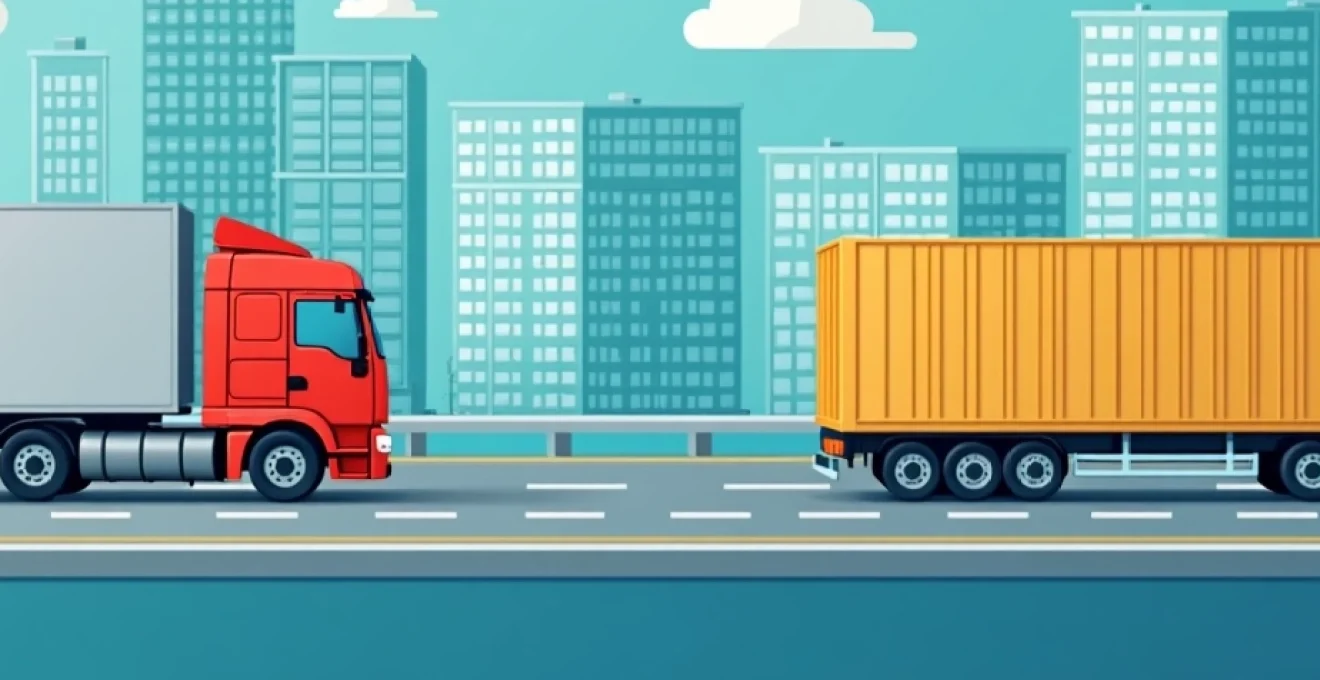
L'optimisation de la chaîne logistique est devenue un enjeu majeur pour les entreprises cherchant à améliorer leur compétitivité et leur efficacité opérationnelle. Une gestion efficace des flux logistiques permet non seulement de réduire les coûts, mais aussi d'accroître la satisfaction client et de s'adapter rapidement aux fluctuations du marché. Dans un environnement économique de plus en plus complexe et dynamique, la maîtrise des processus logistiques s'avère être un véritable avantage concurrentiel. Comment les entreprises peuvent-elles optimiser leur chaîne logistique pour une meilleure gestion des flux ? Quelles sont les méthodes et technologies les plus efficaces pour y parvenir ?
Analyse des flux logistiques avec la méthode SCOR (supply chain operations reference)
La méthode SCOR est un modèle de référence pour l'analyse et l'optimisation des chaînes logistiques. Développée par le Supply Chain Council, cette approche permet d'évaluer et d'améliorer les performances logistiques en se basant sur cinq processus clés : planification, approvisionnement, fabrication, livraison et retour. En utilisant un langage commun et des indicateurs standardisés, SCOR facilite la communication entre les différents acteurs de la chaîne logistique et permet d'identifier rapidement les axes d'amélioration.
L'un des principaux avantages de la méthode SCOR est sa capacité à décomposer les processus logistiques en sous-processus détaillés, offrant ainsi une vision granulaire de l'ensemble de la chaîne. Cette décomposition permet d'identifier avec précision les goulots d'étranglement, les redondances et les opportunités d'optimisation. Par exemple, dans le processus d'approvisionnement, SCOR peut aider à analyser les délais de livraison des fournisseurs, la qualité des matières premières reçues et l'efficacité des procédures de commande.
En outre, SCOR propose un ensemble d'indicateurs de performance (KPIs) couvrant l'ensemble des aspects de la chaîne logistique, de la fiabilité à la réactivité en passant par l'agilité, les coûts et la gestion des actifs. Ces KPIs permettent aux entreprises de benchmarker leurs performances par rapport aux meilleures pratiques du secteur et d'identifier les domaines nécessitant une attention particulière.
L'utilisation de la méthode SCOR peut conduire à des améliorations significatives des performances logistiques, avec des réductions de coûts pouvant atteindre 30% et des augmentations de la satisfaction client de l'ordre de 20%.
Implémentation du lean management dans la chaîne d'approvisionnement
Le lean management, initialement développé dans l'industrie automobile japonaise, s'est progressivement imposé comme une approche incontournable pour l'optimisation des chaînes logistiques. Son objectif principal est d'éliminer les gaspillages ( muda en japonais) et de maximiser la valeur ajoutée à chaque étape du processus. Dans le contexte de la gestion des flux logistiques, le lean management se traduit par plusieurs pratiques et outils spécifiques.
Cartographie de la chaîne de valeur (value stream mapping)
La cartographie de la chaîne de valeur (VSM) est un outil visuel puissant permettant de représenter l'ensemble des flux de matières et d'informations au sein de la chaîne logistique. Cette technique permet d'identifier rapidement les activités à valeur ajoutée et celles qui ne le sont pas, ainsi que les temps d'attente et les stocks intermédiaires. En analysant la VSM, les entreprises peuvent repérer les opportunités d'amélioration et concevoir un état futur optimisé de leur chaîne logistique.
Pour réaliser une VSM efficace, il est recommandé de suivre ces étapes :
- Sélectionner une famille de produits ou un flux spécifique à analyser
- Cartographier l'état actuel en incluant tous les processus et flux
- Identifier les gaspillages et les points de friction
- Concevoir un état futur optimisé
- Élaborer un plan d'action pour atteindre l'état futur
Système kanban pour la gestion des stocks
Le système Kanban, qui signifie "étiquette" ou "carte" en japonais, est une méthode de gestion des stocks basée sur le principe du pull (flux tiré). Dans ce système, la production ou l'approvisionnement est déclenché uniquement lorsqu'un besoin réel se manifeste en aval de la chaîne logistique. Le Kanban utilise des signaux visuels, traditionnellement des cartes, pour indiquer quand il faut réapprovisionner un stock ou lancer une production.
L'implémentation d'un système Kanban peut apporter plusieurs avantages :
- Réduction des stocks et des coûts associés
- Amélioration de la rotation des stocks
- Simplification de la gestion de production
- Réduction des temps de cycle
- Augmentation de la flexibilité face aux variations de la demande
Méthode des 5S pour l'optimisation des entrepôts
La méthode des 5S est une technique d'organisation du travail visant à améliorer l'efficacité et la productivité en créant un environnement de travail propre, ordonné et sécurisé. Dans le contexte de la gestion des flux logistiques, les 5S peuvent être appliqués aux entrepôts et aux zones de stockage pour optimiser l'utilisation de l'espace et faciliter les opérations de manutention.
Les 5S représentent cinq étapes clés :
-
Seiri
(Trier) : Éliminer les éléments inutiles -
Seiton
(Ranger) : Organiser l'espace de travail de manière efficace -
Seiso
(Nettoyer) : Maintenir la propreté des lieux -
Seiketsu
(Standardiser) : Établir des procédures pour maintenir l'ordre -
Shitsuke
(Respecter) : Faire des 5S une habitude quotidienne
Kaizen et amélioration continue des processus logistiques
Le Kaizen, terme japonais signifiant "amélioration continue", est une philosophie qui encourage les petites améliorations quotidiennes plutôt que les grands changements ponctuels. Dans le domaine de la logistique, le Kaizen se traduit par une culture d'amélioration continue où chaque employé est encouragé à identifier et à proposer des améliorations, aussi modestes soient-elles.
L'application du Kaizen dans la gestion des flux logistiques peut prendre diverses formes :
- Ateliers de résolution de problèmes
- Groupes de travail transversaux
- Systèmes de suggestions d'amélioration
- Formations régulières aux outils d'amélioration continue
En favorisant une culture d'amélioration continue, les entreprises peuvent non seulement optimiser leurs processus logistiques, mais aussi développer l'engagement et la créativité de leurs employés.
Technologies de l'industrie 4.0 pour la gestion des flux
L'avènement de l'Industrie 4.0 a apporté une véritable révolution dans la gestion des flux logistiques. Les nouvelles technologies numériques offrent des opportunités sans précédent pour optimiser les opérations, améliorer la visibilité et accroître la réactivité de la chaîne logistique. Parmi ces technologies, certaines se démarquent par leur impact potentiel sur l'efficacité des flux.
Internet des objets (IoT) et traçabilité en temps réel
L'Internet des Objets (IoT) permet de connecter des objets physiques à Internet, offrant ainsi la possibilité de collecter et d'échanger des données en temps réel. Dans le contexte de la gestion des flux logistiques, l'IoT trouve de nombreuses applications, notamment pour la traçabilité des produits et la gestion des stocks.
Les capteurs IoT peuvent être utilisés pour :
- Suivre la localisation des produits en temps réel
- Surveiller les conditions de stockage (température, humidité)
- Détecter les anomalies dans la chaîne logistique
- Optimiser les itinéraires de livraison
- Automatiser la gestion des stocks
Grâce à ces technologies, les entreprises peuvent réduire les pertes , améliorer la qualité des produits et optimiser leurs processus logistiques de manière significative.
Big data et analyse prédictive pour l'anticipation des demandes
Le Big Data et l'analyse prédictive offrent de nouvelles perspectives pour la gestion des flux logistiques. En exploitant de vastes quantités de données issues de sources variées (historiques de ventes, données météorologiques, tendances des réseaux sociaux, etc.), les entreprises peuvent anticiper avec plus de précision les fluctuations de la demande et adapter leur chaîne logistique en conséquence.
L'analyse prédictive permet notamment de :
- Optimiser les niveaux de stocks
- Planifier les approvisionnements de manière plus précise
- Prévoir les pics de demande saisonniers
- Identifier les tendances émergentes du marché
Les entreprises utilisant l'analyse prédictive dans leur gestion des flux logistiques ont constaté une réduction moyenne de 15% de leurs coûts de stockage et une amélioration de 25% de leur taux de service client.
Intelligence artificielle et optimisation des itinéraires de livraison
L'intelligence artificielle (IA) trouve de nombreuses applications dans l'optimisation des flux logistiques, notamment pour la planification des itinéraires de livraison. Les algorithmes d'IA peuvent prendre en compte une multitude de facteurs (trafic en temps réel, conditions météorologiques, contraintes de livraison, etc.) pour déterminer les itinéraires les plus efficaces.
L'utilisation de l'IA pour l'optimisation des itinéraires permet de :
- Réduire les coûts de transport
- Améliorer les délais de livraison
- Optimiser l'utilisation des ressources (véhicules, personnel)
- Réduire l'empreinte carbone des activités logistiques
Blockchain pour la sécurisation et la transparence des transactions
La technologie blockchain, connue principalement pour son utilisation dans les cryptomonnaies, offre également des opportunités intéressantes pour la gestion des flux logistiques. En fournissant un registre distribué, immuable et transparent des transactions, la blockchain peut améliorer la traçabilité des produits et sécuriser les échanges d'informations tout au long de la chaîne logistique.
Les applications potentielles de la blockchain dans la logistique incluent :
- La traçabilité des produits de leur origine à leur destination finale
- La sécurisation des documents de transport et des contrats
- L'automatisation des paiements via des contrats intelligents
- La lutte contre la contrefaçon et les fraudes
Stratégies de gestion des stocks et approvisionnement
La gestion efficace des stocks est un élément crucial de l'optimisation des flux logistiques. Elle permet de réduire les coûts de stockage tout en assurant la disponibilité des produits pour répondre à la demande. Plusieurs stratégies et méthodes peuvent être mises en œuvre pour améliorer la gestion des stocks et l'approvisionnement.
Méthode ABC pour la classification des produits
La méthode ABC est une technique de classification des stocks basée sur le principe de Pareto, qui stipule que 20% des causes produisent 80% des effets. Dans le contexte de la gestion des stocks, cette méthode permet de catégoriser les produits en trois classes :
- Classe A : 20% des produits représentant 80% de la valeur des stocks
- Classe B : 30% des produits représentant 15% de la valeur des stocks
- Classe C : 50% des produits représentant 5% de la valeur des stocks
Cette classification permet d'adapter les stratégies de gestion des stocks en fonction de l'importance de chaque catégorie de produits. Par exemple, les produits de classe A feront l'objet d'un suivi plus rigoureux et d'un contrôle plus fréquent que les produits de classe C.
Modèle EOQ (economic order quantity) pour l'optimisation des commandes
Le modèle EOQ, ou Quantité Économique de Commande, est une formule mathématique permettant de déterminer la quantité optimale à commander pour minimiser les coûts totaux de stockage et de passation de commande. Ce modèle prend en compte plusieurs paramètres :
- La demande annuelle du produit
- Le coût de passation d'une commande
- Le coût de stockage unitaire
La formule EOQ est la suivante :
EOQ = √((2 * D * S) / H)
Où :
- D = Demande annuelle
- S = Coût de passation d'une commande
- H = Coût de
Approche Just-in-Time (JIT) et réduction des stocks tampons
L'approche Just-in-Time (JIT) est une stratégie de gestion des stocks visant à réduire au minimum les stocks tampons en synchronisant parfaitement l'approvisionnement avec la demande. Cette méthode, initialement développée par Toyota, permet de réduire considérablement les coûts de stockage et d'améliorer l'efficacité de la chaîne logistique.
Les principaux avantages de l'approche JIT sont :
- Réduction des coûts de stockage
- Amélioration de la qualité des produits
- Augmentation de la flexibilité de production
- Réduction des gaspillages
- Optimisation de l'espace de stockage
Cependant, la mise en œuvre du JIT nécessite une coordination étroite avec les fournisseurs et une excellente maîtrise des prévisions de demande. Une rupture dans la chaîne d'approvisionnement peut rapidement entraîner des arrêts de production coûteux. Comment les entreprises peuvent-elles alors sécuriser leur approche JIT tout en bénéficiant de ses avantages ?
Collaboration inter-entreprises et supply chain management
La collaboration inter-entreprises est devenue un élément clé de l'optimisation des flux logistiques. Dans un environnement économique de plus en plus complexe et globalisé, aucune entreprise ne peut prétendre maîtriser seule l'ensemble de sa chaîne logistique. La mise en place de partenariats stratégiques et le partage d'informations entre les différents acteurs de la supply chain permettent d'améliorer la visibilité, la réactivité et l'efficacité globale des flux.
Les principales formes de collaboration inter-entreprises dans le domaine de la logistique incluent :
- Le Vendor Managed Inventory (VMI), où le fournisseur gère directement les stocks de son client
- Le Collaborative Planning, Forecasting and Replenishment (CPFR), qui implique un partage des prévisions et des plans d'approvisionnement entre partenaires
- Les plateformes logistiques mutualisées, permettant à plusieurs entreprises de partager des ressources de stockage et de transport
- Les systèmes d'information intégrés, facilitant l'échange de données en temps réel entre les acteurs de la chaîne logistique
La mise en place de ces collaborations nécessite souvent un changement culturel au sein des organisations. Il s'agit de passer d'une logique de confrontation à une logique de partenariat, où la performance globale de la chaîne prime sur les intérêts individuels à court terme.
Mesure de performance et KPIs logistiques
La mesure et le suivi de la performance sont essentiels pour optimiser efficacement les flux logistiques. Les Key Performance Indicators (KPIs) permettent de quantifier les progrès réalisés, d'identifier les axes d'amélioration et de comparer les performances avec les meilleures pratiques du secteur. Voici quelques KPIs clés pour évaluer la performance de la chaîne logistique :
Taux de rotation des stocks et days inventory outstanding (DIO)
Le taux de rotation des stocks mesure la fréquence à laquelle une entreprise renouvelle ses stocks sur une période donnée. Un taux élevé indique une gestion efficace des stocks, tandis qu'un taux faible peut signaler des surstocks ou des problèmes d'écoulement. Le DIO, quant à lui, représente le nombre moyen de jours pendant lesquels les stocks sont détenus avant d'être vendus.
Formules de calcul :
Taux de rotation des stocks = Coût des ventes / Stock moyen
DIO = (Stock moyen / Coût des ventes) * 365
On-time In-Full (OTIF) pour l'évaluation des livraisons
L'OTIF est un indicateur composite mesurant la capacité d'une entreprise à livrer les bonnes quantités de produits, au bon endroit et au bon moment. Il combine deux mesures : le respect des délais de livraison (On-Time) et la conformité des quantités livrées (In-Full). Un OTIF élevé témoigne d'une chaîne logistique performante et fiable.
Calcul de l'OTIF :
OTIF = (Nombre de livraisons conformes en délai et en quantité / Nombre total de livraisons) * 100
Coût total de possession (TCO) dans la gestion des fournisseurs
Le TCO va au-delà du simple prix d'achat pour prendre en compte l'ensemble des coûts associés à l'acquisition, l'utilisation et la maintenance d'un produit ou d'un service tout au long de son cycle de vie. Dans le contexte de la gestion des fournisseurs, le TCO permet d'évaluer de manière plus complète la performance économique des partenaires de la chaîne logistique.
Les éléments à prendre en compte dans le calcul du TCO incluent :
- Le prix d'achat initial
- Les coûts de transport et de manutention
- Les coûts de stockage
- Les coûts de qualité (contrôles, retours, rebuts)
- Les coûts administratifs liés à la gestion de la relation fournisseur
Perfect order rate et satisfaction client
Le Perfect Order Rate mesure le pourcentage de commandes livrées sans aucun problème : à l'heure, complètes, sans dommage et avec une documentation correcte. Cet indicateur est étroitement lié à la satisfaction client et reflète la performance globale de la chaîne logistique.
Calcul du Perfect Order Rate :
Perfect Order Rate = (Nombre de commandes parfaites / Nombre total de commandes) * 100
En complément de ces KPIs quantitatifs, il est important de mesurer régulièrement la satisfaction client à travers des enquêtes qualitatives. Ces retours permettent d'identifier les axes d'amélioration perçus par les clients et de prioriser les actions d'optimisation de la chaîne logistique.
Une étude récente a montré qu'une amélioration de 3% du Perfect Order Rate peut entraîner une augmentation de 1% de la marge opérationnelle pour une entreprise moyenne.
L'optimisation des flux logistiques est un processus continu qui nécessite une vision globale de la chaîne d'approvisionnement, une collaboration étroite entre les différents acteurs et un suivi rigoureux des performances. En combinant les méthodes traditionnelles d'optimisation avec les nouvelles technologies de l'Industrie 4.0, les entreprises peuvent significativement améliorer l'efficacité de leur chaîne logistique, réduire leurs coûts et augmenter la satisfaction de leurs clients. Dans un monde où la réactivité et la flexibilité sont devenues des avantages concurrentiels majeurs, la maîtrise des flux logistiques s'impose comme un facteur clé de succès pour les entreprises de tous secteurs.